Posted March 17, 2022 at 10:36am by Anonymous (not verified)
Vermont Beer Makers Brew up Energy Savings
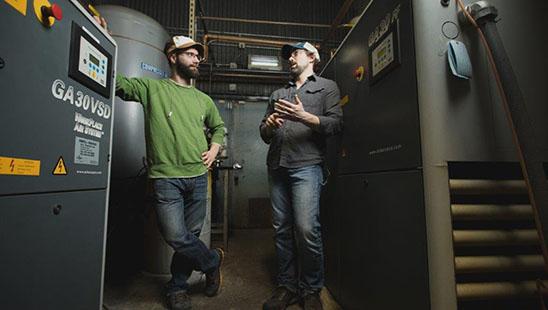
How Vermont Beer Makers Brew up Energy Savings
By Morgan Hood, Efficiency Vermont Account Manager
Big things are brewing at Magic Hat Brewing Company in South Burlington. That’s where skilled beer makers from five Vermont breweries gathered recently with energy efficiency experts from Efficiency Vermont, Burlington Electric Department, and Loureiro Engineering Associates for a three-day intensive dive into energy use. As Magic Hat’s designated energy advisor at Efficiency Vermont, I was fortunate to work alongside this accomplished group of brewers as they learned how to find and address the causes of unnecessary energy use. The time was well spent; the group identified potential energy savings of as much as $320,000 per year for Magic Hat, preventing power-plant pollution equivalent to a year’s emissions from 167 cars.
Efficiency Vermont has the pleasure of leading events like these for a range of industry-specific groups throughout the state. We find that when we bring operations experts from similar businesses together under one roof, we can – together – uncover notable savings opportunities that apply industry-wide. Click here for more information about Efficiency Vermont's Continuous Energy Improvement efforts.
The hunt for savings
Joining Magic Hat for the event were managers and staff members from Drop-in Brewery of Middlebury, Harpoon Brewery of Windsor, Hermit Thrush Brewery of Brattleboro, and Northshire Brewery of Bennington. The group formed five teams – each with an energy advisor – in a hunt for energy savings. Each team had its own focus area:
- Lighting
- Motors, pumps, and production exhaust fans
- Heating, ventilation, air conditioning, and process boilers and chillers
- Compressed gasses
- Thermal energy
A key part of the energy hunt took place after hours, when employees had gone home and the plant was idle. This “sleeping plant” tour is like taking a look inside your refrigerator after the door is shut. Did the light actually go off or did it keep shining needlessly, wasting electricity and even warming up the air temperature? Now imagine that on a much larger scale. We often have found that when facilities aren’t in use, they are very much “awake.” A sleeping-plant tour identifies those systems that can be turned off or dialed back outside of work hours.
The lighting team was particularly successful during the sleeping plant tour, discovering that many of the facility’s 380+ lights stayed on 24 hours per day, every day. The team calculated that lighting accounts for nearly 40% of the brewery’s “baseload,” or the minimum amount of power it uses at any given moment. To put that in perspective: We recommend a 30% baseload for manufacturing facilities, and we’ve found that 20% or less is often achievable with new light-emitting diode (LED) lights and lighting controls.
The lighting team also found that, by establishing protocols for employees to shut off lights at the end of their shifts, Magic Hat will save nearly $5,500 per year. That’s an impressive return on a $0 investment. Add to that upgrades like new LED lights and motion-sensing switches and the total annual savings from lighting efficiency could be as much as $30,000. That’s enough to pay for the upfront cost of the upgrades within 3.5 years.
The combined savings opportunities identified by the five teams yielded impressive numbers:
- Potential electric and natural gas use reduction: 40 percent
- Potential annual savings: $320,000
- Total electricity saved per year: 1.6 million kilowatt-hours – enough to power about 170 Vermont homes for a year
- Total fossil fuel saved per year: 15,344 MMBTUs – enough to heat about 170 Vermont homes for a year
Collaboration makes all the difference
Magic Hat Brewery Manager Robert Kuntz summed up the experience this way:
“Having the other brewers and the consultants on site made all the difference. It’s been showing in our brewery metrics that we had room to improve. It takes a fresh set of eyes to help you focus in on what could be improved. We’ve put a lot of focus on water usage and waste generation, but we needed the extra technical expertise on calculating the wastes in our electrical and steam generation.”
Robert went on to reveal that Magic Hat has since “executed roughly a dozen of the 30+ projects we identified, and most of it was just changing behaviors and funding simple maintenance projects. I’d recommend the process to any brewery in the state. You build relationships with the other brewers and collaborate in a way that isn’t about recipes or brewing process. Together, you give back more to Vermont than just the jobs or the beers – it’s about taking care of the community – down to the water we drink and the air we breathe.”
Green brewers leading the way
The brewers who participated in the Magic Hat event are members of the Green Brewery Cohort (GBC), an initiative developed by the Vermont Green Business Program and Efficiency Vermont. The GBC provides technical and financial support to brewers who are working to reduce their facility’s energy use by five percent by March 2019. Other members of the GBC are Mill River Brewery of St. Albans, 14th Star Brewery of St. Albans, and Whetstone Brewery of Brattleboro.
The committed brewers of the Green Brewery Cohort are clearly off to a great start in their efforts to strengthen their bottom lines and reduce their energy use through energy efficiency. I call that good news for our state’s beer lovers and for the innovative businesses they count on for the nation’s finest brews.
Cover Photo: Testing for compressed-air leaks: Charles Soucy, Hermit Thrush Brewery's Cellars Manager and Sustainability Coordinator with Morgan Hood, Efficiency Vermont Account Manager.
###
This work aligns with Farm to Plate's Goal 22: Food system enterprises will minimize their use of fossil fuels and maximize their renewable energy, energy efficiency and conservation opportunities. You can read more about this here.