Posted March 17, 2022 at 10:36am by Anonymous (not verified)
Efficiency at a Dairy Processor
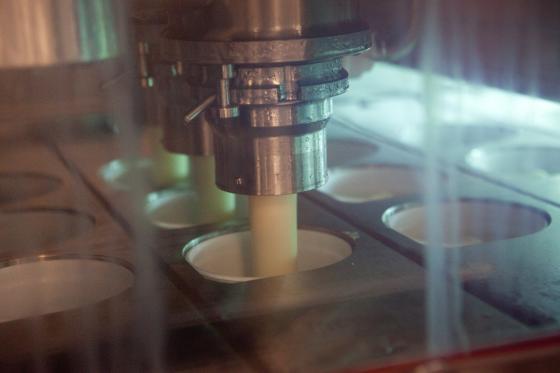
Prepared by JJ Vandette, Planning and Development Associate, Efficiency Vermont
Highlights: $150,000 in first year savings ● $2.1 million in lifetime savings ● 1.5 million in annual kWh savings ● Refrigeration system, compressed air system, motors, lighting, heating, and ventilation optimized
When German Company Ehrman AG partnered with Commonwealth Yogurt, LLC to expand to New England, they were impressed by Vermont’s approach to energy efficiency. That, coupled with a wealth of dairy farms and yogurt enthusiasts, was enough to convince them to break ground in Brattleboro in 2009. Today, the Ehrmann Commonwealth Dairy team sells yogurt under the local brand name Green Mountain Creamery and they also make private label yogurt products for retailers throughout the region and beyond. A major overhead expense is energy, including propane and electricity. Maintaining an energy efficient facility is imperative for any manufacturer and has become even more important in the increasingly competitive yogurt market.
Laying the Groundwork Early for Maximum Energy Savings
By consulting with Efficiency Vermont from the beginning, Commonwealth was able to make strategic choices that continue to benefit them today—and they haven’t stopped there. Though their facility is widely considered to be state of the art due to their extensive control systems and the latest in processing equipment, Commonwealth continues their pursuit of efficiency.
One notable improvement was catalyzed by working with their Efficiency Vermont account manager to assess and adjust their compressed air system, which yielded an annual savings of $22,300. Commonwealth was in need of a backup compressed air system, and after an analysis, recognized that their existing compressed air system was oversized. They purchased a smaller compressed air system for their daily operation and were able to use the existing larger system as the backup. Commonwealth uses compressed air for many parts of their process such as their pneumatic valve clusters—these move product from one point in the process to another—and they pressurize all of their tanks with clean, filtered air in order to keep the product as fresh as possible.
Another notable component of Commonwealth’s efficiency projects was the inclusion of a water-cooled chiller system with variable speeds. This more efficient refrigeration system allowed Commonwealth to meet the requirements of their processes all while using less energy. Other energy efficiency efforts that were undertaken include efficient motors, lighting, heating, and ventilation. Regardless of the size of the operation, employing energy efficiency strategies at a dairy processing facility is most effective when implementing energy saving techniques across various levels of production.
From Overhead to Investment—Putting Energy to Work, Wisely
These ongoing efficiency measures have opened up significant cash flow for Commonwealth, enabling them to expand their operations, distribute more yogurt, and hire more people. Commonwealth is also collaborating with other businesses to ship whey byproducts as biofuel. The byproducts are being used as animal feed for a nearby farmer and in a local biodigester. This effort not only decreases the pressure on the local wastewater treatment facility but it also helps reduce the waste stream and increases the sustainability of their business operations.
Energy can be a significant portion of operating costs for dairy processors and using this energy more efficiently can have a great impact on a processor’s bottom line. “Financially speaking, managing our energy and reducing our usage is hugely important to the success of our company. Energy is one of the top, if not the top, overhead cost that we’re faced with,” says Commonwealth Dairy’s CFO, Ben Johnson. “I know when I am starting any new project in the facility, trying to engage the Efficiency Vermont team to get a good review of what we’re trying to do is part of the project kick off. This allows us to get good suggestions on something we could actually act on, if appropriate.”
“Balancing energy efficiency and capital expenditures is a challenge, which is why the Efficiency Vermont team is such a valuable resource. Efficiency Vermont understands that businesses must realize a payback on their capital investments and they do a great job of laying out the data and presenting the payback realistically.”
—Ben Johnson, CFO, Commonwealth Dairy
Learn more about energy efficiency and renewable energy in the Energy section.