Posted March 17, 2022 at 10:36am by Anonymous (not verified)
Digester on a Dairy Farm
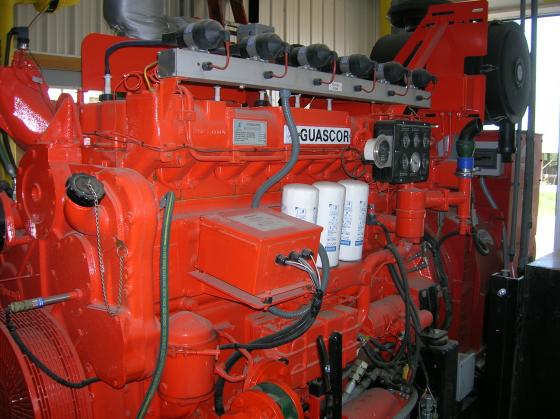
Prepared by Alex DePillis, Senior Agricultural Development Coordinator, Vermont Agency of Agriculture, Food and Markets
Highlights: 225 kilowatts of installed capacity ● 1.75 million kWh of electricity generated per year ● 7-year payback ● Cow Power farm generates electricity and uses waste heat for greenhouse
Lois and Maurice Maxwell started Maxwell’s Neighborhood Farm in 1957. Four sons (Stewart, Bradley, Anthony, and Jeffrey) and a grandson, Matthew, now operate the approximately 800 cow dairy. The Maxwells pursued a methane, or anaerobic, digester as a way to diversify their operation at a time of low milk prices.
Methane digesters are oxygen-free tanks or containers that use microorganisms (i.e., different types of bacteria) to transform biomass like cow manure into “biogas” (e.g., methane and carbon dioxide), while retaining the manure slurry. This biogas can then be fed to a gas engine to generate electricity, or to a boiler to generate heat. In 2008 the Maxwells partnered with the Green Mountain Power Cow Power program to build a digester system and incorporated it as Maxwell’s Neighborhood Energy. There are currently 12 dairy farms enrolled in the Cow Power program.
Equipment Costs, Energy Payments, and System Payback
The total cost of this project was about $1.8 million. A $100,000 grant from GMP was coupled with a $357,990 grant and a $326,770 loan guarantee from the USDA Rural Energy for America Program (REAP), $250,000 from the Vermont Clean Energy Development Fund, and $75,000 from the Vermont Agency of Agriculture. Because the farm was connected to Vermont Electric Coop through single-phase electric power—and the engine-generator is three-phase electric power—over $78,000 was paid to upgrade 1.6 miles of utility lines. Maxwell Neighborhood Energy is paid for the electricity generated by the Vermont SPEED program, at the farm methane rate of $0.14 per kilowatt-hour. In addition, customers enrolled in the Cow Power program pay an additional 4 cents per kilowatt-hour for the environmental attributes of the energy produced, and this money goes to the farmer.
With the combination of electricity sales, reduced heating costs, and animal bedding savings and sales, the Maxwells believe the system will be paid off in a little over seven years. However, Vermont dairy farmers with digesters and technical assistance providers also caution that digester equipment, particularly the engine-generator, require significant attention to detail and technical issues need to be addressed promptly to avoid long-term problems.
Digester Characteristics
Maxwell’s Neighborhood Energy worked with GHD (now DVO) for the digester design and installation, Martin Machinery for the 225 kW Guascor engine-generator package, and many subcontractors.
The digester measures 72 feet wide by 96 feet long by 16 feet deep, and is a U-shaped configuration. It holds almost 800,000 gallons and is large enough to retain incoming manure for about three weeks. The Maxwells also contract with a food processing facility in Maine for additional liquids to put in their digester (about 10% by volume) and this boosts gas production by about one-third.
After three weeks in the digester the manure odor is virtually neutralized. Liquid separated from the manure during the digestion process becomes easier to spread—and odorless. And the fertilizer value present in the manure going into the digester is still available after this “aging” process. Biogas from the digester is cooled to remove moisture, and sent to the 225-kilowatt engine-generator, which can produce enough electricity for about 200 homes. During this process, methane produced from animal waste—a greenhouse gas 20 times more powerful than carbon dioxide—is captured and destroyed. If there is too much gas, or the engine is being serviced, gas is sent to a flare to be burned off.
Additional Benefits
The engine-generator includes heat exchangers that deliver useful amounts of heat for space heating beyond the heat needed to keep the digester warm. The Maxwells decided to transfer some of the digester’s excess heat through plastic piping in the ground over to a greenhouse—installed in the winter of 2013. These pipes heat both the ground and the air inside the greenhouse.
Matt Maxwell manages the greenhouses and grows greens all fall and winter. As spring approaches, he transitions from greens to tomatoes. For about six weeks, Matt is able to sell beautiful, ripe, early-season tomatoes for about four dollars a pound into the local market.
As Matt readily points out, selling electricity is only part of the picture. Matt also harvests peat-moss-like bedding from the digester. The bedding suits the cows very nicely, and while it saves money compared to buying sawdust, it’s hard to put a price on the peace of mind that comes from knowing that they don’t have to skimp on bedding and that their cows are well cared for and healthy. This bedding can also be used as a soil amendment in the greenhouse. Matt is able to compost some of the bedding and sell it to landscaping companies and other gardeners. The Maxwells also save on wood and other purchased sources of heat that used to heat the maintenance shop and the milkhouse, since the heat from the engine-generator is now displacing those fuels.
Learn more about energy efficiency and renewable energy in the Energy section.